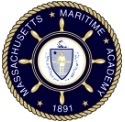
Assessment OICEW-5-1L
Prepare main steam turbine for operation
Assessed in EN-4231 Sea Term IV: Marine Engineering
Recommended Turbine Start-up Procedure (TS Enterprise Specific)
Line up and Start Main Lube Oil System:
- Check that Lube Oil temperature is 90° F
- Check that alarm signal panel is energized
- Test low gravity tank alarm
- Test lube oil pump failure alarm
- Test low lube oil pressure alarm
- Line up selected lube oil cooler
- Line up motor driven lube oil pump
- Open lube oil fill/dump valve to lube oil gravity tank
- Start motor driven lube oil service pump
- Start lube oil standby pump in standby mode
- Insure lube oil pump failure alarm reading normal
- Insure lube oil gravity tank alarm is reading normal
- Insure lube oil low pressure alarm is reading normal
- Inspect all engine lube oil sight glasses to insure visual flow
- Verify lube oil flow in bull's eye
- Check that no leaks exist in the lube oil system
Place into Service Jacking Gear:
- Open all turbine casing drains
- Verify lubrication of bearings and gears
- Check all spring bearings and insure proper lube oil level
- Check stern tube packing gland for slight leakage and tightness
- Confirm no obstructions exist around propeller
- Request permission from bridge to start jacking gear
- Remove padlock and pin
- Rotate lever to engaged position
- Push pin through lever and replace padlock to secure pin
- Start jacking gear motor
- Place "Jacking Gear Engaged" sign on main throttles
- Record main engine thrust readings in engineroom log book
Line up and Start Main Circulating system:
- Open main condenser overboard valve
- Open suction valve to main circulating pump
- Start main circulating pump in low speed
- Vent main condenser heads
Line up and Start Main Condensate System:
- Open suction, vent, gage and sealing line to main condensate pump
- Open condensate recirculating valve one full turn
- Start the main condensate pump and open the discharge
- Monitor D.C. heater level and auxiliary exhaust pressure
Line up and Start Gland Seal System
- Open gland exhaust valve from engine to gland exhaust condenser
- Drain down and admit steam to glands using gland seal regulator bypass
- Place into service gland seal regulator and adjust to maintain 1/2 to 2 psig
Line up and Start Air Ejector and raise vacuum
- Select either port or starboard set of main air ejectors
- Open 1st and 2nd stage air ejector suction and discharge valves
- Admit steam to 2nd stage nozzle
- At 16-20 inches Hg apply steam to 1st stage nozzle
- Monitor air ejector steam pressure, adjust as necessary at regulator
Applying steam to the engine (placing into service):
Caution needs to be taken to insure gradual warmup of main steam lines and the throttle valve assembly. Prior to admitting steam to the throttle valve assembly fully open and lightly seat the ahead and astern throttle and inspect and linkage.
- One hour prior to receiving standby, warm up main steam line by opening bypasses on the main steam stop and bulkhead stop valves
- Open all throttle drains
- Receive permission from bridge to roll the engine
- Stop and disengage the Jacking Gear
- Remove "Jacking Gear Engaged" sign from throttles
- Align throttle drains to D.C. Heater
- Slowly open main steam and bulkhead stop valves
- Insure 19 nozzles configuration to HP turbine are open
- Open astern guarding valve
- Open astern throttle first and confirm engine rpms (No more than 10)
- Alternate ahead and astern throttle no more than 10 rpms
- Continue until steam line temperature to HP turbine is 500 degree F.
- Do not let hot rotor stand still for more than five minutes
- Insure all proper personnel are present for maneuvering
- Notify bridge that engineroom is ready to "answer all bells"
- Establish time of "stand-by engines" with bridge
- Close casing drains at first half-ahead bell
Condition
In an approved simulator or aboard a ship in port or at anchor, given access to a main steam turbine.
Performance Requirements
Behavior | Standard |
---|---|
The student will: | During assessment, the student shall, at a minimum: |
Verify stern tube and line shaft lube oil Verify minimum lube oil temperature Verify oil flow to all bearings Verify gravity tank overflow | |
Place into service jacking gear |
Check for propeller obstructions and obtain wheel clearance Hang jacking gear engaged sign |
Verify coolant flow | |
open main condensate pump vent and seal adjust main condensate recirculating valve monitor dc heater level | |
line up gland exhaust adjust gland seal regulator to 1.5 psig | |
Direct steam to second stage Raise vacuum to approximately 20 inches Hg |
Supports Table A-III/1 officers in charge of an engineering watch
Competence | Knowledge, Understanding & Proficiency | Task |
---|---|---|
Operate main and auxiliary machinery and associated control systems |
A4.1 Basic construction and operation principles of machinery systems, including:
|
Prepare main steam turbine for operation |